The Blast Furnace Is Under Reconstruction after Twenty-two Years
The reconstruction of the primary metallurgical production technology started a few days ago in Třinecké železárny. The repair and reconstruction of one of the two blast furnaces numbered #6 is currently underway. After 62 days, on 19 October, the blast furnace operators will blow it out again and start melting pig iron.
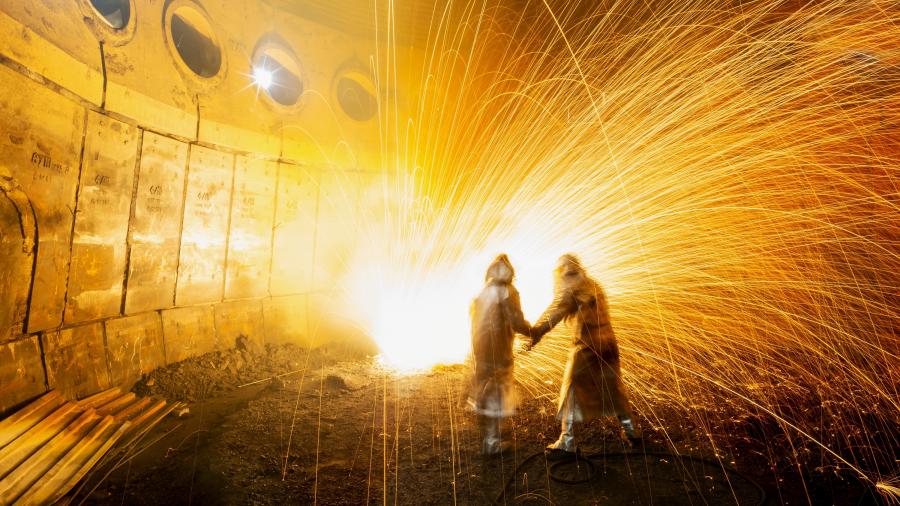
It is the largest investment of this year. The total cost of reconstruction and repairs will amount to CZK 650 million. It is a technologically and logistically very demanding project with regard to minimizing production downtime. The last overhaul of BF #6 took place in 1999, 22 years ago. Since then, the furnace has produced over 22 million tons of pig iron.
The primary objective of the refurbishment is to install new elements and process equipment in line with current trends. This will make pig iron production more efficient and reduce the environmental burden. "The essential point of the project is the renovation of the blast furnace with new carbon blocks and the installation of new refractory linings," explains Česlav Marek, the Production Director. He adds that the simultaneous start of operation of the third and last in the series Kalugin type hot blast stove, whose reconstruction the company started several months ahead of schedule, will be quite crucial for the operation of the furnace.
"Thanks to the installation of modern hot blast stoves together with the installation of new air preheating assemblies, the consumption of blast furnace gas for heating the stoves will be reduced and the production of blast furnace gas itself will be reduced. This will result in a reduction in CO2 emissions. In the context of our commitment to a low-carbon future, this is one of the essential steps in the reconstruction," adds Investment Director Radek Olszar.
Annually, the furnace produces more than one million tons of pig iron, which is sent for further processing to the steel plant and then to the rolling mills of Třinecké železárny, where specific products or semis are produced. The average daily capacity is 3,000 tons.
Fun Facts of the Reconstruction
The crucial moment of the start of the repairs was the so-called blowing out of the furnace, when the raw materials stopped being loaded into the furnace and the charge gradually dropped to the bottom of the furnace by gradually reducing the air blowing.
Now the replacement of the linings and the installation of new carbon blocks will begin. The material for the new linings arrived at the company earlier in the year. This is about 1,000 tons of material. Interesting is also the delivery of a special cooler for the blast hole, which came to Třinec from far away South Africa. It is a copper casting that only a few non-ferrous foundries in the world can produce. What makes it special is that the purity of the copper casting is 99.8% copper. In our foundries, a copper casting of about 93 to 97% copper purity can be made.
Fun Facts on Blast Furnace #6
- 69 years in operation since 1952.
- Overhauls carried out in 1963, 1973, 1985 and 1999.
- Since 1999, it has produced over 22 million tons of pig iron.
- The cost of repair and reconstruction is estimated at 650 million crowns.
- 1000 tons will be the total weight of the new blast furnace.
- 48 tribal employees work here (dozens more take care of the two furnaces in maintenance, electrical maintenance, control systems, conveyor belting, including masons and technicians).
Petra Macková Jurásková
Press Secretary of the Třinecké železárny - Moravia Steel Group
phone: +420 558 535 841
mobile: +420 602 265 738
e-mail: Petra.Mackova@trz.cz
Třinecké železárny – Moravia Steel
phone: +420 558 535 841
mobile: +420 602 265 738
e-mail: Petra.Mackova@trz.cz